We designed and built a brake burnishing machine for one of our core customers in Indiana. A new ANSI standard requiring all forklift brakes be burnished prior to sale drove the project. Our customer reached out to us confident we would be able to complete it and deliver by the compliance date. In just a few months we had the machine designed, built and proven out with a few weeks to spare.







The operator scans a barcode containing the order number for the part. The data is relayed to an SQL database, then program information and target parameters for that part are sent back to the machine. After loading the part in the machine, an Omron IO-Link laser distance sensor mounted on an IAI Robocylinder measures and compares the height of the brake assembly in the machine against a target value received from the database. This is used as a pokayoke to ensure the operator has used the correct jig fixture for the part.

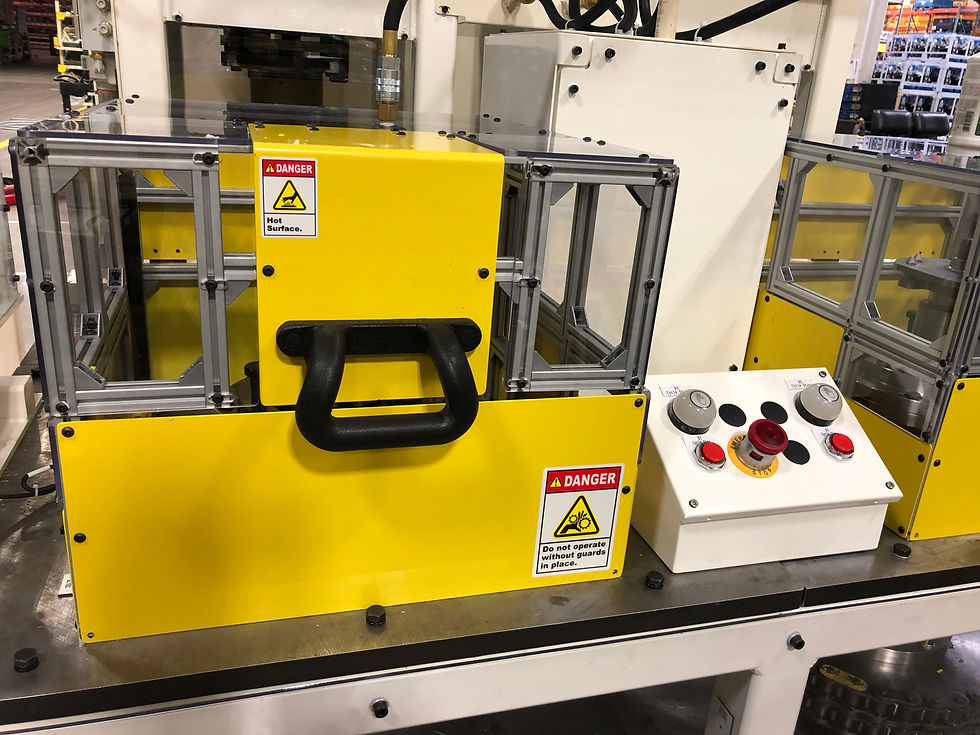

The machine uses Analog Load Cell feedback for PID control of an Omron 1S Servo Motor in Torque Mode to simulate pressing the forklift’s brake pedal. This is similar to a Servo Press, but customized to allow the Servo Motor to hold a specified Brake Pedal Force for an extended period. A Mitsubishi A800 series Inverter turns the drum as output torque is monitored via another Kyowa Load Cell, thus ‘breaking in’ the brake pads until a desired torque is achieved—Torque representing the stopping ability of the forklift. Results from each process and test are then sent back to the SQL Database to be stored for quality purposes.
Comments